弯 管 机
自动弯管机的模弯曲是一种钢管在弯曲模型中实现弯曲的成形过程,它包括压弯、推弯和绕弯三种方式。
1.压弯
压弯早用于管材弯曲加工的工艺方法。如图1-2所示,它是在液压机上利用模具或胎具对管坯进行弯曲加工。压弯方法既可以弯制带直段的管件,又可以弯制弯头。山于压弯具有生产效率高、模具调整简单等突出优点,故在生产中一直被广泛应用。
2.推弯
推弯是在一般压力机、液压机上进行弯曲加工,主要用于弯制弯头。推弯包括型模式冷推弯管和芯棒式热推弯管。型模式冷推弯管是在普通液压机或曲柄压力机上,利用金屈的塑性,在常温状态下将管坯压入带有弯曲型腔的型模中,从而形成弯头。型模式冷推弯管装置如图1—3所示。芯棒式热推弯管是在专用推制机上,在推力和牛角芯棒阻力的作用下,边加热边推制,使管坯产生周向扩张和轴向弯曲变形,从而将较小直径的管坯推制成较大直径的弯头,其工作原理如图1-4所示。
3.绕弯
绕弯是常用的弯管方法,包括辗压式和拉拔式,工作原理如图1-5所示。按照弯管设备的不同,绕弯又可以分为手工弯管和弯管机弯管两类。
根据不同客户的需求,管材的弯制也是各有特点,而弯管机也因为品种的不同为有不同的弯管过程,这里主要讲的就是自动弯管机的弯管过程:自动弯管机的弯管过程是先向机床内置计算机输入导管的成形数据,然后放置管坯,由机床自动控制弯曲成形。为此,首先需制出导管实样,通过对实样测量得出原始管形数据,再把数据传输到自动弯管机的PC机中,然后修正管形数据,使弯制的导管与实样一致。
自动弯管机弯管的主要的一步是是参数的确定,导管弯管前除弯曲半径外,还需确定以下参数:
(1)直线段AB的长度。
(2)弯曲角度BCD,即第二条直线段与第一条直线段之问的夹角。
(3)直线段DE的长度,两圆弧之间的切点距离。
(4)空间转角Ot,即第二个弯所在平面与第一个弯所在平面的夹角,即ACF平面与CFI平面的夹角。
(5)弯曲角度EFG,即第三条直线段与第二条直线段之间的夹角。
(6)直线段GH的长度,两圆弧之间的切点距离。
(7)空间转角 是第三个弯所在平面与第二个弯所在平面的夹角,即CFI平面与FIK平面的夹角。
(8)弯曲角度 K是第四条直线段与第三条直线段之间的夹角。
利用数控自动弯管机弯曲摩托车上几个主要复杂管件获得成功,累了丰富经验右扁平端弯曲前应在压力机上经成形、切边冲 孔、冲小漏水孔等工序成形。弯曲时用扁平端 在弯管机上一方面作辅助夹持用,另一方面作定 位、定向用。该零件属空间立体形状,具有三维 坐标,三个实际弯形部位,弯曲不完全在一个平面内。零件作为车架右侧主管,与左侧主管 此呈右、左对称分布各一件.其上焊接有管件、冲压件等数十件。
弯管机进行管材的弯曲和板料的弯曲一样。在纯弯曲的情况下,外径为D,壁厚为t的管子受外力矩 M的作用发生弯曲时,中性层外侧管壁受拉应力σ1作用,管壁变薄;中性层内侧管壁受拉应力σ1作用,管壁变厚。而且,横截面的形状由于受合力F1和F2的作用由圆形变为近似椭圆形,当变形量过大时,弯管机外侧管壁会产生裂纹,内侧管壁会出现起皱。管材的变形程度,取决于相对弯曲半径R/D和相对厚度t/D数值的大小。R/D和t/D值越小,表示变形程度越大。为保证管件成形质量,必须控制变形程度在许可范围内,管材弯曲成形极限不仅取决于材料的力学性能和弯曲方法,而且还考虑管件的使用要求。
在西气东输管道工程中, 冷弯管是将管道直接进行物理弯曲, 管道材质没有破坏性变化, 因此在长输管道建设中具有独特的优势。中小型冷弯管机预制的是直径较小的钢管, 对机械本身的要求不高, 但在西气东输工程中
弯管机管材弯曲加工在工程机械、动力机械以及锅炉、石油化工、管道工程等领域占有十分重要的地位,管材空心横截面的形状特点给弯管设备的设计带来诸多工艺问题。
冰芯自动弯管机技术属机加工技术领域。它是在所需弯曲的管材内灌水或加绳灌水后冷冻成冰芯后弯曲,成型后化冰,放水即可。它工艺成本低,产品质量高,经济效益好。冰芯弯管技术的特征在于在所需弯曲的管道内置入草绳后灌水,封闭后冷冻,把结成冰绳芯的管件在弯曲机上弯曲后,待冰化后打开封闭端,放出水与草绳即可。
一种弯曲金属圆管的冷形方法其特征在于采用钢丝制成的一根密绕簧作为充填物,其直径略小于管坯内径,弹簧钢丝的直径为管坯壁厚的1.5至3倍,弹簧的一端向心弯一小勾,勾长度为弹簧的半径,管坯经退火处理后,在管坯内部涂一层机油(或黄油)将弹簧放入,其长度与管坯长度相同。经弯管机按所需曲率半径对金属管坯施压弯曲,然后用取簧器夹住小勾顺弹簧卷绕方向绕出内填弹簧,整个成形过程在冷态下一次完成。
自动弯管机进行管材的弯曲和板料的弯曲一样。在纯弯曲的情况下,外径为D,壁厚为t的管子受外力矩 M的作用发生弯曲时,中性层外侧管壁受拉应力σ1作用,管壁变薄;中性层内侧管壁受拉应力σ1作用,管壁变厚。
冲压弯头加工是借助于常规或专用冲压设备的动力,使板料在模具里直接受到变形力并进行变形,从而获得一定形状,尺寸和性能的产品零件的生产技术。板料,模具和设备是冲压加工的三要素。冲压加工是一种金属冷变形加工方法。所以,被称之为冷冲压或板料冲压,简称冲压。它是金属塑性加工(或压力加工)的主要方法之一,也隶属于材料成型工程技术。
冲压弯头制作工艺的优点主要表现在以下几个方面:
冲压弯头适用于石油、天然气、化工、水电、建筑和锅炉等行业的管路系。 不需管坯作原料,可节约制管设备及模具费用,且可得到任意大直径而壁厚相对较薄的碳钢弯头。由于上述二条原因,可以缩短制造周期,生产成本大大降低。因不需要任何专用设备,尤其适合于现场加工大型碳钢弯头。坯料为平板或可展曲面,因而下料简单,精度容易保证,组装焊接方便
由于自动弯管机的管件大多数用于焊接,为了提高焊接质量,端部都车成坡口,留一定的角度,带一定的边,这一项要求也比较严,边多厚,角度为多少和偏差范围都有规定,几何尺寸上比管件多了很多项。表面质量和机械性能基本和管子是一样的。为了焊接方便,和被连接的管子的钢种是相同的。第四,就是所有的管件都要经过表面处理,把内外表面的氧化铁皮通过喷丸处理喷掉,再涂上防腐漆。
这既是为了出口需要,再者,在国内也是为了方便运输防止锈蚀氧化,都要做这方面的工作。第五,就是对包装的要求,对于小管件,如出口,就需要做木箱,大约1立方米,规定这种箱子中的弯头数量大约不能超过一吨,该标准允许套装,即大套小,但总重量一般不可超过1吨。对于大件就要单个包装,像24″的就必须单个包装。另外就是包装标记,标记是要注明尺寸、钢号、批号、厂家商标。在管件上要打上钢印,并附有装箱单和质保书等文件。大小头生产工艺简单,生产效率高,成本低,发展较快。大小头生产的主要原材料在大小头生产成本中占有很大比例,其价格的变化直接影响生产成本的变化。
弯管机适用于工厂、仓库、码头、建筑、铁路、汽车等按装管道和修理。它除了具有弯管功能外,还能卸下弯管部件(油缸)作为分离式液压起顶机使用。若采用同类型的不锈钢冲压弯头焊接,必须进行300℃以上的预热和焊后700℃左右的缓冷处理。若焊件不能进行焊后热处理,则应选用大小头焊条。大小头的强度一般比直缝焊管高,能用较窄的坯料生产管径较大的弯头,还可以用同样宽度的坯料生产管径不同的焊管。
自动弯管机操作前,首先检查各润滑点是否缺油,运动机构是否松动,安全防护装置是否可靠,待确认后方可操作。起动油泵,系统压力是否保持在规定范围内,若高,损伤液压元件,浪费电源,若过低,影响工作。
无芯弯管的工作原理与有芯弯曲相似。由于其省略了芯棒,为了对弯曲回弹进行补偿,一般在管坯进入弯曲变形之前要进行反变形处理。即利用反变形滚轮或滑槽对管坯施以适当的压紧预变形。在弯曲后,相反方向的变形相互抵消,使管材横截面基本能够保持圆形。
全自动弯管机过去,手工弯管常常采用20、30号机油作润滑剂。对于润滑剂的质量和数量没有引起足够的重视。进行数控弯管时,由于弯曲的速度较快,芯棒和管壁产生的磨擦力很大,一般的机油不能在其中间形成油膜,达到润滑的目的。因而在弯曲过程中,产生“吭…吭…”尖叫声,并伴随着有波纹产生。这当然与芯棒的提前量和芯棒杆的抖动等因素有关。但当芯棒提前量适当,芯棒杆有足够的刚性时,与润滑剂的质量和数量有重要关系。
在弯曲过程中,润滑剂必须在管子内壁和芯棒之间形成润滑油膜,全自动液压弯管机并且润滑剂必须均匀覆盖管子内表面。在弯管机上配有芯棒润滑装置,即在进行每一个DOB时,一个气泵将润滑剂通过芯棒杆和芯棒上的孔,挤入管子内腔。在生产中,可用“拉伸油”作润滑剂。在没有拉伸油时,我们自己配制了一种润滑剂,也能够满足弯曲需要。
标弯头成型技术基本工艺过程是:首先焊接一个横截面为多边形的多棱环壳或两端封锁的多棱扇形壳,内部冲满压力介质后,施以内压,在内压作用下横截面由多边形逐渐变成圆, 国标弯头能够在建筑行业中施展重要的作用和贡献,表现好的机能上风,展现重要的作用和价值。国标弯头于弯管不同,在出产和制作工艺中据有不同的特点和机能,采用不同的工艺和方式进行出产和加工。国标弯头与弯管的区别顾名思义在本质上是“头”和“管”的其别,但是在制作工艺上却有很大的不同
目前,世界上有美国、加拿大和德国等发达国家近10家冷弯机生产厂,所产机型基本结构均为垂直液压式,内胎形式主要有气动式和液压式两种。气动式结构内胎优点在于行走速度快、弯管预制效率高,但需要另行配置空气压缩机,系统工作平稳性差,难以控制。液压式内胎借助于整机液压站,结构紧凑,且液压传动平稳可靠,能够保证管道在预制过程中不发生椭圆变形。
在原有导管实样不能利用的情况下,决定对该型号飞机上所用的能上数控自动弯管机的导管零件进行标准实样的重取和规范,并根据数控自动弯管机和配套弯管模的情况,以及导管的空间走向,按照导管的材料规格和弯曲半径进行分类,确定329个图号的弯管上数控弯管机生产。在完成该机型导管实样的重新弯制后,按储存在弯管机中的导管成形的基本数据进行批量生产,所生产的导管空间走向合格,且质量好。但复制出的导管实样绝大多数不合格,究其原因主要是由导管弯曲半径不规范导致的。
在数控弯曲管材过程中,由于弯曲中J}生层外侧的切向拉应力作用,外侧减薄是不可避免的。但自动弯管机管壁厚度过度减薄必然降低管件的承载能力,影响管件的使用性能,严重时甚至导致开裂,故壁厚减薄是影响数控弯管质量的一个主要因素。影响管弯曲壁厚减薄的因素很多,芯棒是其中一个重要因素H 在有芯弯曲中,芯棒伸出量对管壁变薄也有重要影响。
随着芯棒伸出量的增加,管材弯曲过程中的壁厚变薄率变化趋势可分为3个阶段,即线性下降阶段、过渡阶段和非线性增加阶段。有芯弯曲中弯曲速度对壁厚变薄率的影响表现为:当弯曲速度在较小范围内增加时。壁厚变薄趋向于减小;当弯曲速度增加到一定值时,壁厚变薄率达到小值,如继续增加弯曲速度。壁厚变薄率将增加。
夹头是卡紧管子和支承管子用的,它与摇臂通过燕尾导轨连接.夹头的宽度一般取管子的直径, 因此,弯管机上各有几种规格的夹头, 以适应加工不同直径管材时配用.夹头的张开与夹紧是用液压油缸或液压马达带动丝杠来完成的。夹头的径向移动是由单独的液压马达带动丝杠来实现的。导向辊轮是管子定心装置,并承受弯曲时产生的作用力。它由两对导向辊轮和移动驱动部分组成.其中,一对导向辊轮是V形面,另一对是圆弧面.
高频加热线圈是用紫铜(含铜99.9%)材料特殊制做的空心管子(截面可以是圆形或方形)煨割而成的。工作时,其空腔内通有冷却水或空气.并从有一定角度的小孔中喷出射向被加热的弯管上. 以冷却弯管.
自动弯管机设备的维护和保养
1、在清洗油箱时,要清洗各泵的进油滤清器。
2、设备开始使用后的1—2个月內,清洗油箱和过滤一次液压箱。
3、检查各部位紧固件,使之处于紧固狀态。
4、如发现前进与撤退退切失灵,首先检查电磁阀是否动作如电磁阀动作正常,再检查順序阀6X3、溢流阀YF—L20H4或单向卸荷阀4HD3有否杂质卡死现象。 (这种现象一般在设备开始使用时,轻易发生)。如有卡死现象,拆开用汽油或柴油清洗好后,重新裝好即可。
5、液压泵站部位各接头都装有耐油橡胶密封圈、如密封圈损坏、漏油、应及时更换。
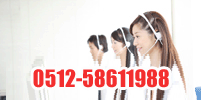
张家港市和力机械制造有限公司
公司电话:0512-58611988
公司传真:0512-58903579
公司邮箱:hyp@hlwgj.com
公司地址:张家港市南丰镇建工大道27号